
Today, advances in numerical schemes andĮnhanced hardware have lead to many commercial codes that can employ Geometries is important, and has perplexed modelers utilizing conventional The need to accurately simulate various physical processes in complex Meshless method is simple, accurate, and requires no meshing. Problems in complex geometries that may require extensive meshing. Methods have been historically used to model a wide variety of engineering Receiving attention in the engineering and scientific modeling communities.įinite difference (FDM), finite volume (FVM), and finite element (FEM) Problems, the meshless method is a particularly attractive method that is
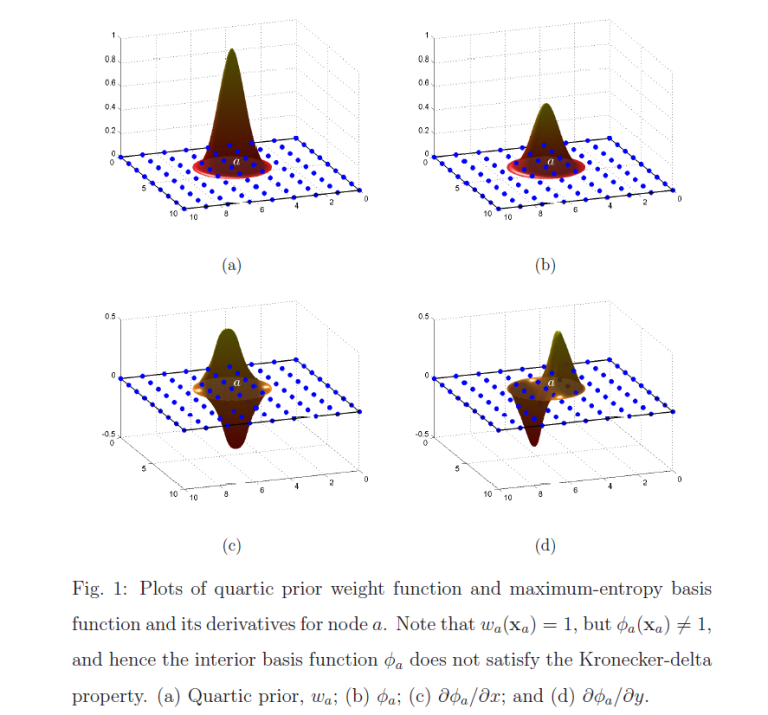
Darrell Pepper, Nevada Center for Advanced Computational Methods, University of Nevada, Las Vegas, USAĪlthough many numerical and analytical schemes exist for solving engineering In the present work, we discuss the current needs for virtual tool optimisation, the limitations of existing simulation software and the potential advantages and disadvantages of Lagrangian particle-based approaches especially SPH.Prof. Based on the SPH, a solver with multi-GPU acceleration for modelling solid materials has been developed, and is proven to be effective in several practical applications involving large deformation and material failure. During the deformation process, previously interacting particles may leave each other's influence domains and cease to interact further which makes SPH natural in handling large material deformation. The Bell-shape of the kernel function ensures that the interaction is at a maximum between immediate neighbours and gradually decreases with an increase in distance between interacting particles. A given particle interacts only with its neighbouring particles through a kernel function whose support is defined by the smoothing length. In SPH the computational domain is discretised by a set of particles.
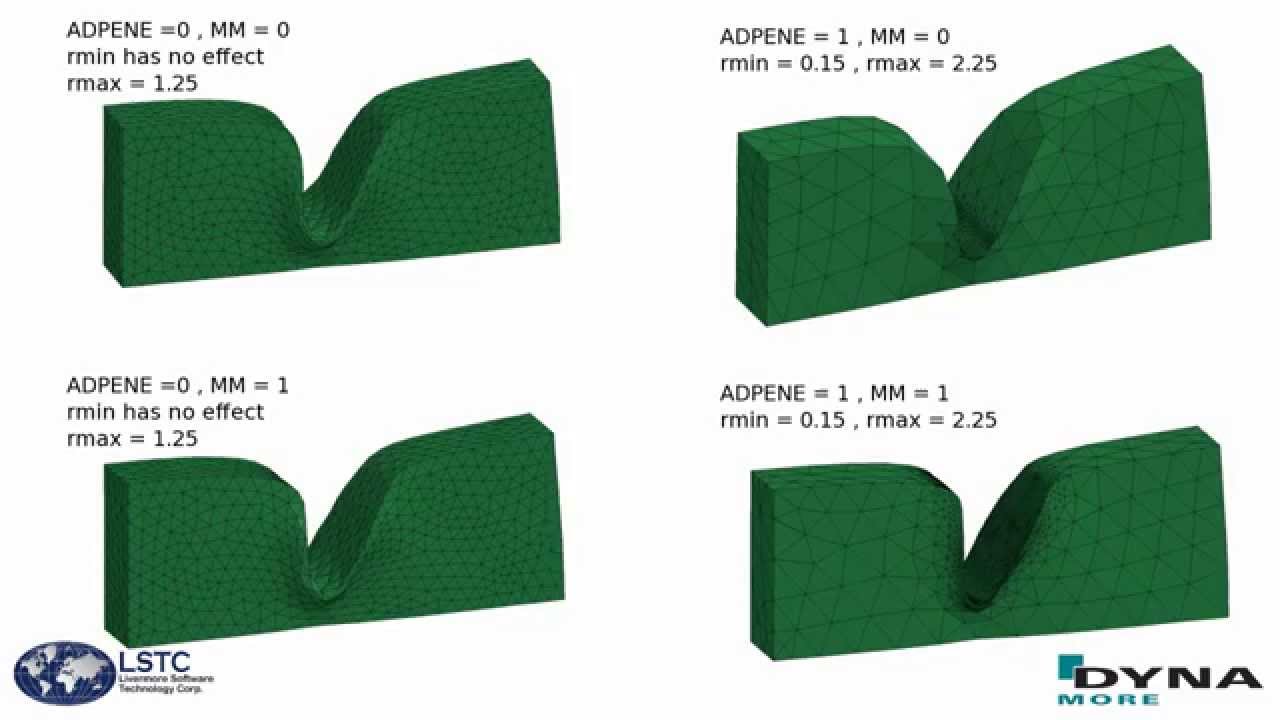
Among them, smoothed particle hydrodynamics (SPH) is entirely meshfree and naturally equipped to handle large material deformation. Very promising alternatives to the Eulerian methods are meshfree Lagrangian methods. Grid-based methods are not naturally equipped to deal with such situations due to the mesh distortion, mesh entanglement and requirement of mesh refinement. Especially the solids undergoing large deformation and the subsequent material separation and propagating cracks demonstrate the limitations: variables become discontinuous across the crack surface, and the computational domain loses its continuum nature. Even some numerical Eulerian approaches (grid-based) exist for modelling solid materials under dynamic loading, most of them are not very successful. The virtual optimisation of tooling equipment is nowadays one of the common challenges in mechanical serial production.
